Quality Control
every product goes through proper inspection and testing procedures before it leaves the plant. The wide range of quality checks are both in-process and prior to shipment. Standard procedures from point-to-point checks of routine test for each panel. The final inspection is performed to check, whether the equipment’s are properly installed.
Our clients are confident in the quality of our manufactured panels; our rigorous factory testing procedures ensure that every assembly unit is functioning at an optimum level before customers receive their product. Our Quality Control Policy is strictly comply with IEC standards.
Failure of electrical switchgear can cause fires, serious injury and major damage for human life and equipment. Strong procedures, preventive actions and involving the quality inspector QCI in each process of production usually maintain switchgear safely and reduce the risk of accidents.
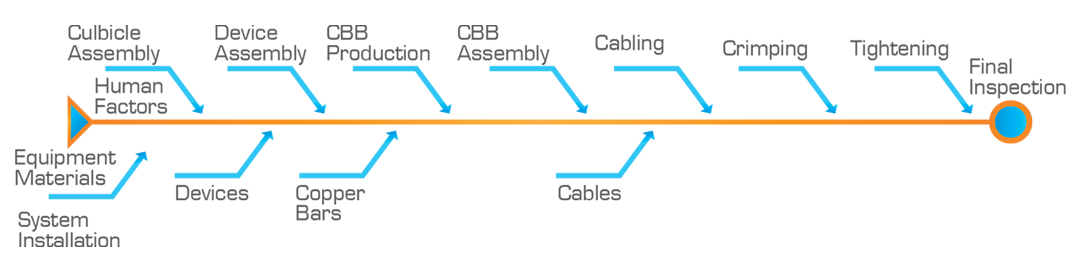
Each process of production must be checked and take the below action:
- At each stage of the Assembly Process, the Quality Control Inspector (QCI) should check if the assembly is in accordance with the approved drawings and assembly rules.
- For any Non-Conformities noticed by QCI, a Non-Conformity Report (NCR) has to be raised to production manager to be rectified.
After all assembly stages are completed, the panels are offered for final inspection and testing that contented the following:
- Visual Inspection Test.
- Di-Electric Test (Voltage Withstand).
- Insulation Resistance Test (Megger)
- Mass Continuity Test
- Operation Test
- Checking of the complete switchboard in accordance to design & approved drawings.
- Checking of Integrity of Wiring, Tightness of all joints, and Torque test on all bus connections, etc.
- The dielectric voltage withstand test is an integral part of the product safety evaluation of low-voltage systems, and provides manufacturers with important information regarding the quality and appropriateness of the chosen insulation system.
- The test involves placing an extra-high voltage between the line to line for one minute.
- This can create a shock hazard if the defects are not corrected at the factory.
Rated insulation voltage Ui | Dielectric test voltage | |
---|---|---|
Main Circuit | 300 V < Ui y 690 V 800 V < Ui y 1000 V |
2500 V 3500 V |
Auxilizry Circuit | Ui y 60 V Ui > 60 V |
1000 V (2 Ui + 1000) V with 1500 V min |
3. Insulation Resistance Test (Megger)
- This test is verified by applying DC voltage between phases, phase-neutral, phase-earth, and neutral-earth which is used to calculate the resistance of the insulation.
- The most important reason for testing insulation is to insure public and personal safety to protect the system against leakage currents miswired.
Nominal voltage (V) | Dc measuring voltage (V) | Insultation resistance (M) |
---|---|---|
< 250V | 500 | ≥ 25 |
=600V | 1000 | ≥ 100 |
>600V | 1000 | ≥ 500 |
4. Mass Continuity Test
- Continuity test is used to insure the operation of the protection devices for both ON/OFF mode.
5. Operation Test
Applying the required voltage trough test bench to verify:
- The required operation voltage.
- Checking the signaling and lights.
- Checking the operation of the motorized parts.
- Simulating the control schemes.